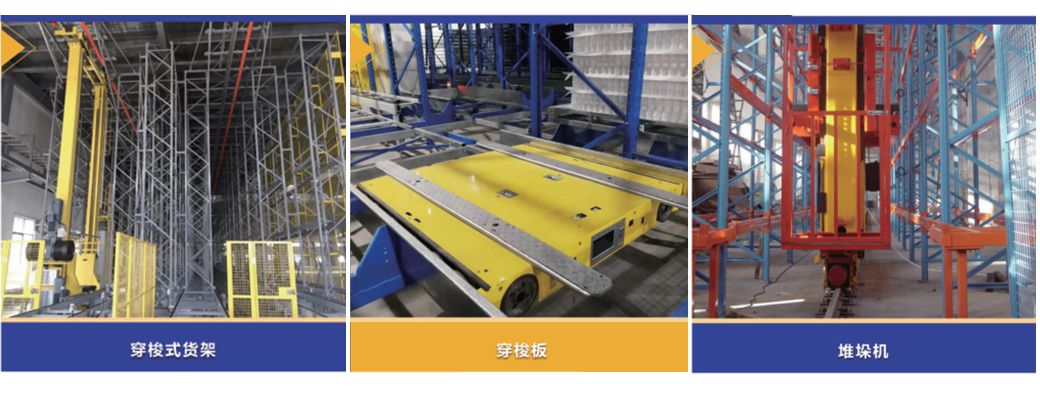

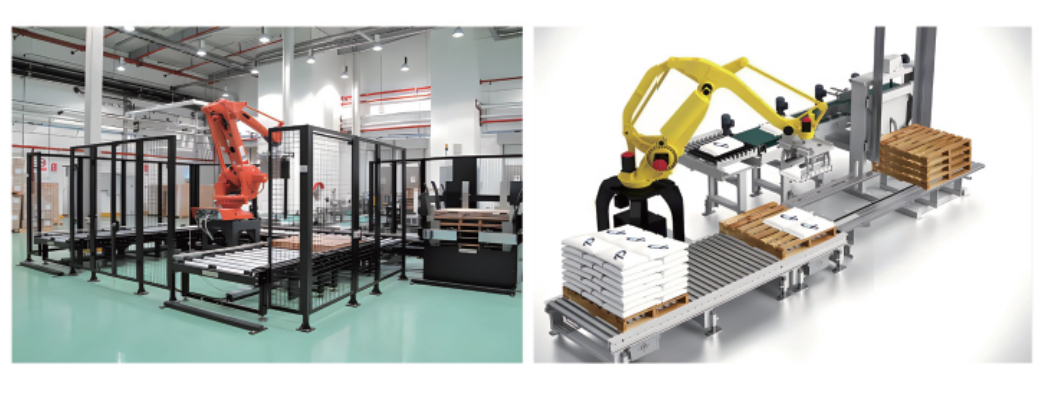
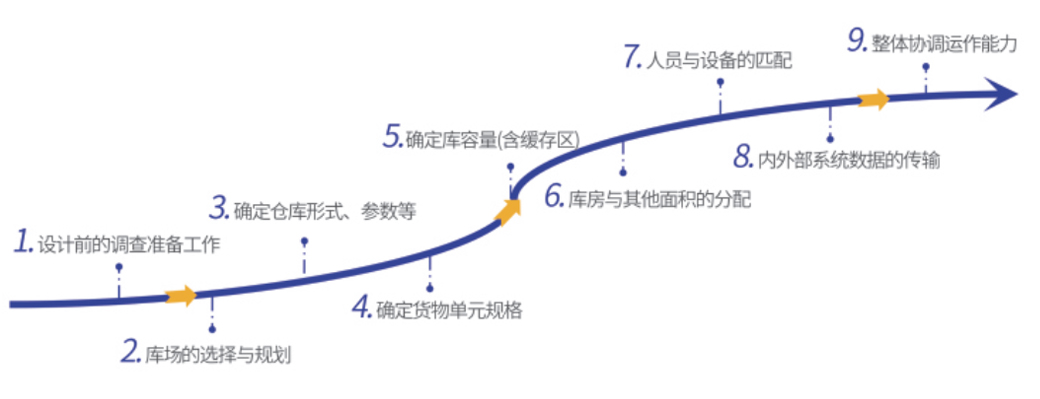
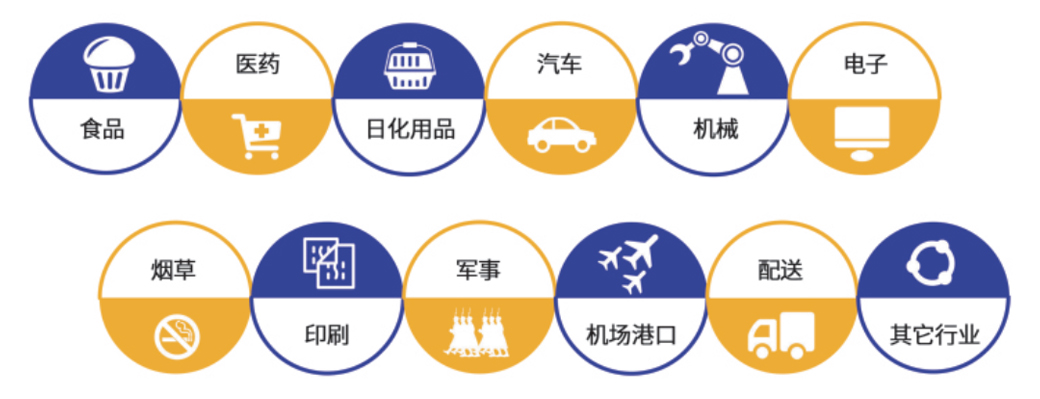
Efficient use of space with high-rise shelves and three-dimensional storage significantly increases the utilization rate of space; automated operations, through automated equipment and technology, achieve automatic storage, retrieval, and management of goods, reducing labor costs; intelligent management, equipped with an advanced warehouse management system, to achieve real-time monitoring and precise management of goods; improving operational efficiency, automated operations reduce manual intervention, increasing the speed and accuracy of operations; enhancing safety, reducing human operational errors, effectively preventing damage and loss of goods.
Warehouse, Fire Protection System, Lighting System, Ventilation and Heating System, Power System, Drainage Equipment, Lightning Protection and Grounding Facilities, Environmental Protection Facilities, etc.
Shelves, Goods and Pallets, Aisle Cranes, Stacker Cranes, Conveyor System, Sorting Equipment, Automated Guided Vehicles (AGVs), etc.
Detection devices, information identification devices, control devices, monitoring and dispatching equipment, computer management systems, data communication equipment, large screen displays, and image surveillance equipment.
Based on the user's process characteristics and requirements, the area can be reasonably divided and increased or decreased.
Pallet Intensive Storage Solution is a storage form based on pallets as the storage unit, with the Warehouse Management System (WMS) acting as the decision-making brain and the Warehouse Control System (WCS) as the command center. Intelligent equipment such as stacker cranes, shuttle robots, and high-precision automated warehouses serve as the execution bodies. Through the organic integration of software and hardware, and scientific scheduling, it achieves automatic goods dispatch, meeting customers' needs for high-density, high-efficiency, and low-cost logistics storage.
With the widest application range, it is widely used in pharmaceuticals, chemicals, textiles, photovoltaics, new energy, agriculture, and more.
In various industries, intelligent factory workshops feature line-side warehouses, smart storage for finished goods, semi-finished products, raw materials, as well as smart logistics centers, showcasing the integration of advanced technology into manufacturing and supply chain management.
The Bin-based Dense Storage Solution employs bins as the fundamental storage unit, featuring an intricate system architecture where the Warehouse Management System (WMS) acts as the decision-making 'brain', orchestrating storage and retrieval operations. The Warehouse Control System (WCS) serves as the 'command center', coordinating the activities of various intelligent devices. These include Multi-level Shuttle Robots, High-speed Quad-directional Shuttle Robots, Rapid Lifts, and Precision Bin-type Automated Storage and Retrieval Systems (AS/RS), which function as the 'execution arms'. Through seamless integration and unified management by information systems, this solution enables efficient handling of small-volume, high-frequency, and fast-turnover goods, facilitating their smooth entry and exit from the warehouse, as well as their selection and sorting processes.
New Energy Lithium Batteries, Electricity Meters, Current Transformers, Wires and Cables, Hardware Parts, Electronic Products.;
Various industry component warehouses, semi-finished goods warehouses, line-side warehouses, and distribution transit warehouses, etc.
Logistics warehousing is a new concept that refers to a warehousing operation system capable of storing and retrieving containerized unit goods and managing them with computers.